Benefits of glass-glass modules
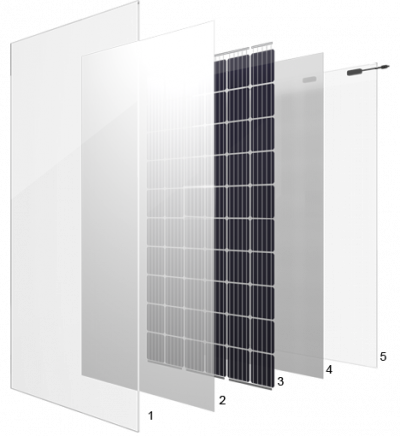
The usual structure of PV modules is a laminate consisting of a sheet of toughened glass 3 to 4 mm thick on the front side, and a flexible polymer sheet on the back side. To ensure sufficient rigidity an aluminum frame must be added. Industrial techniques today make it possible to temper thinner glass, which makes it possible to produce panels composed of a double layer of glass without being too heavy, and rigid and solid enough not to need an aluminum frame.
1. tempered front glass, 2 & 4: POE encapsulant, 3. cells, 5. tempered or hardened rear glass
Benefits of frameless panels
Installers have preferred framed panels to this day, because with the mounting systems available on the market, installation is simpler and faster than for frameless panels. In addition, with the photovoltaic industry heavily focused on standardization and mass production, framed panels have established themselves as the market standard. This is obviously a shame for investors and operators of solar power plants, who cannot benefit from the objective advantages of frameless panels.
Based on this observation, Suncell has developed different mounting systems suitable for frameless panels, which allow rapid, safe and economical mounting of this type of panel.
Bifacial modules

Over the past 12 years the photovoltaic industry has been able to improve the efficiency of photovoltaic modules thanks to technological advances with an average increase of 1.5% per year. In this perspective the appearance of bifacial panels represents a real disruption. By using the same stable crystaline cell technology, and simply making the 2 sides photosensitive, you can get up to 35% more electricity with what is known as Bifacial Boost. However, the module must be mounted in a specific way in order to take full advantage of the bifacial boost.
1. direct irradiation; 2. diffuse irradiation; 3. indirect irradiation reflected by the ground/roof albedo
Our online tool
Suncell® solar systems
Suncell® has developed a range of mounting systems specially designed for frameless panels, which will be marketed in summer 2020. For each installation the complete system, including the panels and the mounting system, is sold with a comprehensive guarantee.
Bifacial system for flat roofs, guaranteeing a bifacial boost > 20%, patent pending
BIPV system, roof integrated – replacing tiles, Terra-cotta or anthracite colored modules
BAPV system for residential roofs, black visual appearance
BAPV system for industrial corrugated sheet roofs, black visual appearance
Made in Europe
Simple and fast planning with PV Designer 3D, with export of drawings in 2D and 3D vector format
Glass printing techniques with ceramic inks today make it possible to produce photovoltaic panels of all colors, but lead to still too high performance losses, often of more than 25%, which is technically and economically unsatisfactory.
Suncell has developed optimized industrial glass preparation processes, focusing on the few most common colors in the built environment (terra-cotta, brown, anthracite, gray), in order to be able to produce colored photovoltaic panels at a cost close to normal premium panels, and with the objective of a performance loss limited to 10%.
Solar glass production
It has to be ultra-clear glass, i.e. with a very low content of iron oxides which reflect solar irradiation
An anti-reflective coating must be applied, on one hand to allow a harmonious integration into the envelope of the buildings, on the other hand so that a maximum of solar irradiation crosses the glass instead of being reflected
Is must be tempered in order to withstand mecanical/physical contraints
The complexity of the manufacturing process for colored solar glass is that printing with special semi-transparent inks must be done before tempering the glass. The integration of these operations into the production flow of our industrial partners allows us to be independent of conventional solar glass suppliers. We therefore have total flexibility in terms of formats, both in terms of tempering and lamination, so that we can, for example also produce very large panels for facades.